Aluminum welding is a key skill in various industries, from automotive to aerospace, due to aluminum’s lightweight and corrosion-resistant properties. However, welding aluminum poses unique challenges due to its high thermal conductivity and low melting point. This blog will guide you through the essentials of how to weld aluminum, providing insights into overcoming common challenges and achieving strong, durable welds.
Understanding Aluminum Welding
Before diving into the specifics of welding aluminum, it’s essential to understand the properties of aluminum that affect its weldability:
- High Thermal Conductivity: Aluminum conducts heat quickly, which means it can dissipate heat from the weld area rapidly. This requires higher heat inputs during welding compared to steel.
- Low Melting Point: Aluminum alloys melt at around 600°C, much lower than steel. This can lead to a high risk of burn-through if not careful.
- Oxide Layer: Aluminum naturally forms an oxide layer that is much higher in melting point than the underlying metal. This layer needs to be removed for successful welding.
Selecting the Right Welding Method
The most common methods for welding aluminum are Gas Tungsten Arc Welding (GTAW, or TIG) and Gas Metal Arc Welding (GMAW, or MIG). Here’s how they compare:
- TIG Welding: Ideal for thin materials and fine, detailed work. It gives the welder greater control over the weld than other methods, making it perfect for high-quality, precise welds.
- MIG Welding: Better suited for thicker aluminum pieces and faster welding speeds. It’s generally easier to learn and more forgiving than TIG, though it can be less precise.
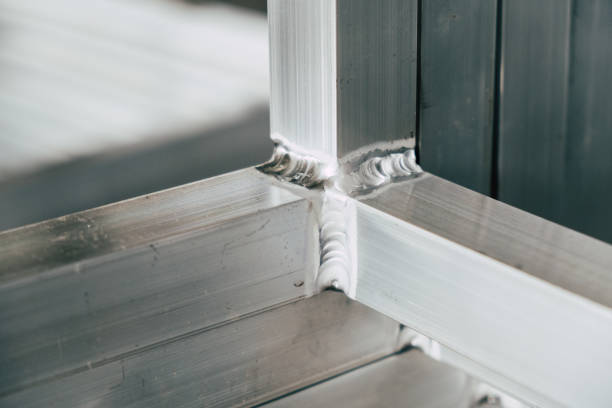
Equipment and Preparation
To start welding aluminum, you’ll need the right equipment. For TIG welding, you’ll require:
- AC capable TIG welder
- High-frequency start capability
- Pure tungsten or zirconiated tungsten electrode
- Argon shielding gas
- Appropriate filler material, 4043 alloy (Al-Si) and 5356 alloy (Al-Mg) are commonly used filler metals
For MIG welding:
- A MIG welder with an aluminum-compatible drive system
- Argon or argon-helium mix for shielding gas
- A spool gun or push-pull gun to prevent wire feeding issues
Preparation is critical when welding aluminum. Clean the material thoroughly to remove any oil, dirt, and especially the oxide layer. Mechanical removal (steel brush) or chemical methods can be used to ensure the aluminum is free of contaminants before you start.
For more information on aluminum welding, please refer to ‘Aluminum Welding: A Practical Guide‘
Welding Techniques
- Preheating: Depending on the thickness and type of aluminum, preheating can help manage the heat dissipation and avoid thermal distortion.
- Push Technique: When MIG welding, use a push technique, where the torch is angled in the direction of the weld, pushing the puddle along. This provides better gas coverage and cleaner welds.
- Puddle Control: Aluminum’s fluidity means managing the weld puddle is crucial. Be attentive to the weld pool’s size and behavior, adjusting your speed and power accordingly.
Troubleshooting Common Problems
- Porosity: This can be caused by contamination, incorrect shielding gas, or too much moisture. Ensure everything is clean and dry and that you’re using the right type and amount of gas.
- Cracking: Aluminum is prone to cracking, especially at the end of the weld. To prevent this, ensure the joint is adequately designed and the material is preheated if necessary. Adding filler material at the end of the weld can also help.
- Distortion: Due to its thermal properties, aluminum can warp dramatically when welded. To combat this, use proper joint preparation, fixtures, and tack welds to hold everything in place.
Wrapping Up
Welding aluminum requires understanding its unique properties and adapting your techniques to accommodate them. With practice, the right equipment, and a thorough preparation process, you can master the art of aluminum welding, making everything from simple repairs to complex assemblies possible. Whether you choose TIG or MIG methods, patience and precision will lead you to successful and strong welds in this challenging but rewarding material.