Battery shell aluminum foil plays a pivotal role in modern battery technology, particularly in lithium-ion batteries, nickel-metal hydride batteries, and other high-performance energy storage systems.
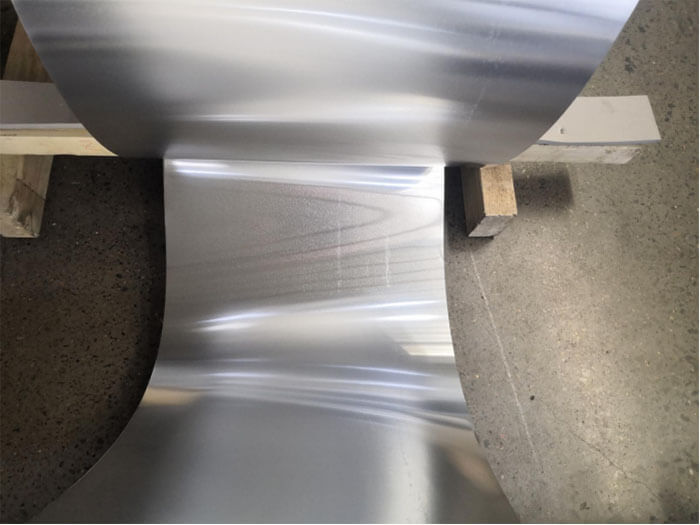
Where to Use Aluminum Foil for Battery Cases
Aluminum foil is employed in the construction of battery cases for:
- Lithium-ion Batteries: For their lightweight, high energy density, and flexibility.
- Nickel-Metal Hydride Batteries: Offering a robust alternative for applications requiring high discharge rates.
- Other Battery Types: Including pouch batteries and square battery casings.
The foil serves as a protective layer within the battery casing, preventing the ingress of moisture and oxygen, which could degrade battery performance over time.
Why Use Aluminum Foil for Battery Cases?
- Corrosion Resistance: Aluminum naturally forms an oxide layer, providing excellent resistance to corrosion, which is crucial for maintaining the integrity of the battery case.
- Conductivity: Aluminum’s high electrical conductivity ensures efficient current flow, enhancing battery performance.
- Lightweight and Ductile: Its properties allow for easy shaping and forming, accommodating various battery designs.
- Thermal Management: Aluminum helps in dissipating heat, preventing overheating and ensuring safety and longevity.
Types of Battery Aluminum Foil
Here are some common types of aluminum foil used in batteries:
- Plain Aluminum Foil: High-purity, uncoated foil for basic conductivity and mechanical support.
- Coated Aluminum Foil: Enhanced with coatings like carbon or polymer for improved conductivity, adhesion, and chemical stability.
- Textured Aluminum Foil: Features a textured surface to increase the electrochemical reaction area, improving battery capacity.
- Ultra-Thin Aluminum Foil: For lightweight and flexible batteries, with thicknesses as low as a few micrometers.
- Laminated Aluminum Foil: Multiple layers bonded for enhanced strength and resistance to mechanical damage.
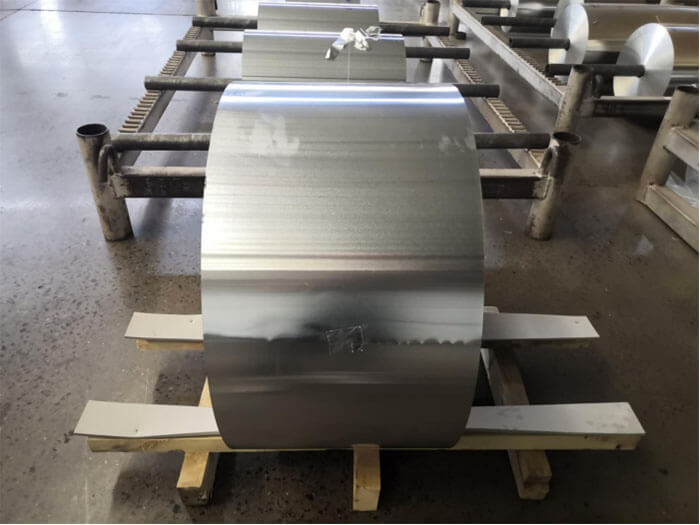
Comparison of Aluminum Foil Alloys:
Alloy |
Temper |
Tensile Strength (Mpa) |
Elongation (%) |
Thickness Tolerance (mm) |
1235 |
H18 |
170-200 |
≥1.2 |
±3% |
1060 |
H18 |
165-190 |
≥1.2 |
±3% |
1070 |
H18 |
≥180 |
≥1.2 |
±3% |
Advantages of Battery Aluminum Foil
- Excellent Physical Properties: High conductivity and corrosion resistance extend battery life.
- Soft and Easy to Process: Simplifies electrode manufacturing, reducing costs.
- Protects Current Collectors: Enhances battery stability by preventing mechanical and chemical damage.
Mechanical Properties and Electrical Resistance
- Tensile Strength: Varies by alloy and temper, typically ranging from 150 to 200 N/mm².
- Elongation: Ensures flexibility and resistance to breakage.
- Electrical Resistance: Decreases with increasing thickness, from 0.55 Ω.m at 0.0060 mm to 0.25 Ω.m at 0.16 mm.
Table: Electrical Resistance by Thickness
Thickness (mm) |
Resistance (Ω.m) |
0.0060 |
0.55 |
0.0070 |
0.51 |
0.0080 |
0.43 |
0.0090 |
0.36 |
0.010 |
0.32 |
0.11 |
0.28 |
0.16 |
0.25 |
Quality Requirements for Battery-Grade Aluminum Foil
- Surface Uniformity, Cleanliness, and Smoothness: Ensures optimal performance and longevity.
- No Rolling Defects: Prevents issues like creases and stains that could impact battery life.
- Consistent Color: Prevents variations that might affect battery consistency.
- No Oil Contamination or Stains: Maintains cleanliness for optimal performance.
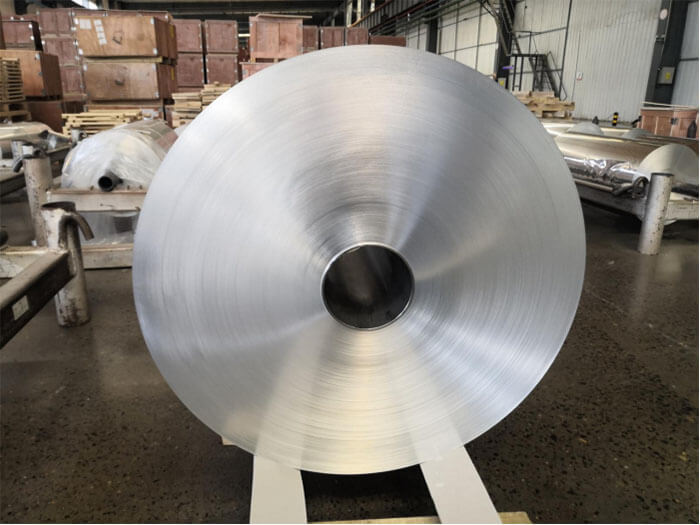
Manufacturing Process of Battery Aluminum Foil
- Casting: Aluminum is melted and cast into blocks or logs.
- Hot Rolling: Reduces thickness at high temperatures.
- Cold Rolling: Further reduces thickness at room temperature.
- Annealing: Enhances flexibility and strength.
- Finishing: Trimming, surface treatment, and quality control.
- Slitting and Packaging: Prepares the foil for distribution.
Frequently Asked Questions about Battery Case Aluminum Foil
- Can any aluminum foil be used for battery cases? No, specific alloys and specifications are required for optimal performance.
- How does aluminum foil contribute to battery safety? By providing corrosion resistance, aiding in thermal management, and ensuring consistent conductivity.
- What should I do if I notice corrosion on the aluminum foil? Investigate the root cause and consider using more resistant alloys or protective coatings.